Words from the coordinator
After 4.5 existing years, the SisAl Pilot project is coming to an end. These years have been filled with lots of labs and pilot-scale experiments both in pyro and hydro, intense discussions about LCA and future business cases, and last but not least incredible memories from project meetings around the globe. It has been a pleasure and lots of joy to coordinate the amazing SisAl team and get to know all the fantastic people involved in the project. Together we have made this project as a success!
Highlights from the WPs:
WP1 Raw Materials: SINTEF and Orykton (subcontractor) assembled an extensive raw materials map for SisAl. This has given us a better understanding of scrap market and the type of Al scrap being exported from Europe and the pricing for potential silica and lime sources.
WP2 Aluminothermic reduction: 3 large pilots for MG-Si/AlSi (Elkem, RWTH, Mintak, FRey, Wacker, Erimsa, and Hydro) and 1 medium-scale pilot for SoG-Si (Silicor and RU) have shown that this is not just possible in small scale but also in large scale! We have also managed to illustrate challenges in refractories, tapping, etc. which is invaluable for scale-up activities. Also complex, next level modelling of reactors and processes has been done (SIMTEC and CITMaga).
WP3 Slag valorization/Alumina production: 2 very challenging pilots!!
• Alkaline route (METLEN, NTUA, NTNU): Next level (from the EU-funded projects Ensural (ID#: 958307) and Removal (ID#: 776469)) understanding of the challenges (SiO2, CaO/Al2O3 ratio etc) in obtaining MG-Al2O3 from SisAl slag.
• Acidic route (METLEN, NTUA and SiQAl): Pioneering work on successful production of 4N HPA.
WP4 and WP5 Environmental and Economic assessments: Seamless collaboration to secure best possible/relevant assessments of environmental and economic performances (BNW-Energy, NTNU, HZDR, SBC and DOW). A special thanks to Befesa for providing LCA Al recycling data!
• Learnings from constructive «arguments» on system boundaries, allocations of environmental loading, CAPEX etc.
• Landing CAPEX for non-industrial processes is not trivial…
• Parameter sensitivity studies are often more constructive/valuable than attempts at exacting values
• Continuously developing/updated process flowsheets are essential for both E&E assessments
WP6 Communication and Dissemination: CTECH and INNEN has kept us up to date on social media/on-line and showed us off at various opportunities, kept a record of our dissemination and communication activities. Also, a special thanks to Science Business and NTNUs Brussels office for helping us organising the thought-proactive roundtable event titled “Critical raw materials and circular economy: A new way forward for Europe?”.
Thanks again for this incredibly journey!
Maria Wallin and Gabriella Tranell
Final project key achievements and results
In the last period of the project the National Technical University of Athens and METLEN Energy and Metals, focused their efforts in extracting high added value product from the SiSAl slag, the by-product of the novel Silicon production method. The SiSAl slag consists mainly of calcium and aluminium oxides. The target was to achieve the extraction of the aluminium from the slag in the form of HPA (High Purity Alumina), aluminium oxide (Al2O3) with purity levels above 99.99% or 4N. In its predominant application, HPA is converted into synthetic Sapphire-crystals used as substrates for Light Emitting Diodes (LEDs) or as scratch resistant protection for watches and smart phones. Further uses are ceramic separator sheets of high-performance Li-ion Batteries (LIBs). Finally, HPA is an irreplaceable material in ultra-niches such as specialty abrasives & ceramics, spinel’s and phosphors, where it fetches the highest price. The strongest future growth for HPA is expected to be for LEDs and LIB separators. HPA is typically produced by dissolution of high purity aluminium metal at a high financial and environmental cost (given that primary aluminium metal production is among the most energy intensive metallurgical industries).
NTUA optimized a method for dissolving the SISAL slag in concentrated HCl solution and then precipitating the aluminium content by HCl gas purging. Through control of the purging process (temperature, time, pressure), NTUA has able to establish the conditions where aluminium was precipitating selectively over the other metals in the solution, thereby producing a pure precursor for HPA.
The process was scaled up from labscale to pilot scale at METLEN, where more than 500 kg or SiSAl slag where leached and more than 50 kg of HPA precursor were eventually precipitated. Once the precursor was calcined to remove chemically bound water and HCl molecules, an HPA product with purity 99,9939% to 99,9962% was produced.
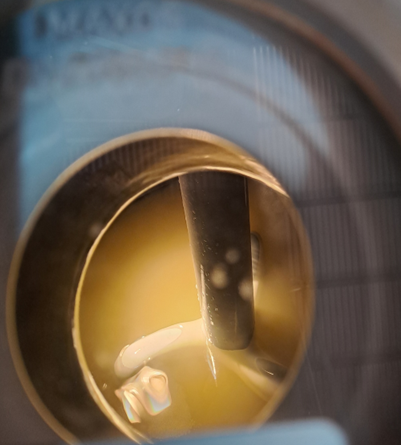
Precipitation of ACH from slag leach solution through HCl gas purging @ METLEN
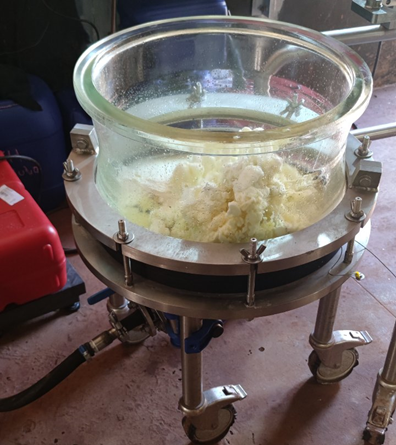
Produced ACH after solid/liquid separation @METLEN
MINTEK demonstrates SisAl process by producing silicon metal with a carbon-free reductant.
Mintek, South Africa’s national mineral and metallurgical research institution, is actively involved in developing and demonstrating sustainable pyrometallurgical processes and technologies. The need to increase the sustainability of pyrometallurgical processes and technologies significantly increases the urgency to develop and demonstrate flowsheets with improved energy and resource efficiency as well as reduced waste and effluent emissions, including demonstrating flowsheets that can incorporate alternative carbon-free reductants. Mintek’s Pyrometallurgy Division recently completed a campaign to demonstrate the SisAl process by utilizing a carbon-free reductant to produce silicon metal.
The SisAl Pilot project was undertaken in collaboration with numerous consortium partners from Europe and South Africa, and was funded under the European Union’s Horizon programme. The process focuses on the production silicon and silicon alloys from secondary silica-containing materials by using secondary aluminium sources as reductants. Mintek pilot test work demonstrated aluminothermic reduction smelting of a calcium-silicate slag through addition of solid aluminium bars.
The pilot campaign was carried out in Sep-Oct 2024 whereby ~3800 kg of silica and ~8000 kg of limestone was smelted in a 3 MW DC arc furnace to produce over 9000 kg of calcium-silicate slag.
Although the test work demonstrated hot transfer of molten slag from DC furnace directly into a top blown rotary converter (TBRC), most of the aluminothermic reduction reactions were demonstrated in the TBRC by first re-melting crushed pre-fused calcium-silicate slag. A 500 L TBRC with a 600 kW oxy-fuel burner was utilized as the reactor for the reduction reactions.
Relatively pure aluminium bars (~99% Al) were added to a pool of slag in the TBRC to produce silicon alloys with average grade of about 70% Si. The exothermic reactions released sufficient energy, to supplement energy from the burner, to heat the product calcium-aluminate slags to temperatures above 1650ºC.
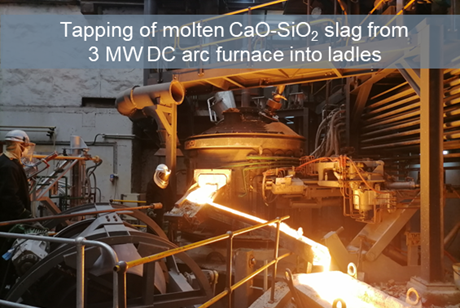
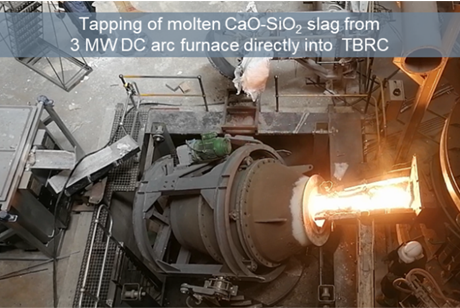
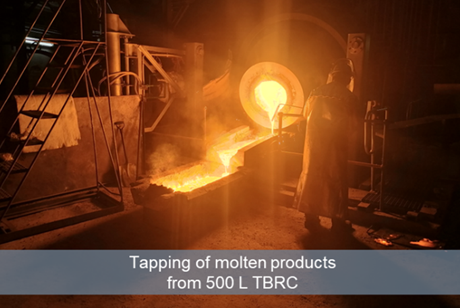
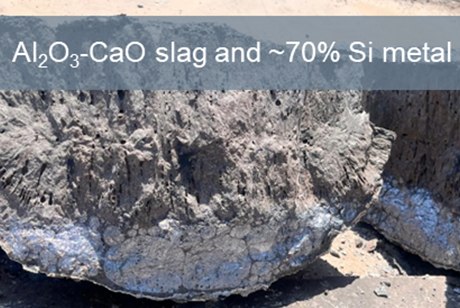